All operations are managed thanks to SAP / ERP management which allows a careful and timely management of all business issues.
The management of incoming or stock materials (managed with FIFO logic) takes place through the reading of the bar code that allows traceability in real time.
All production and storage areas are EPA (Electrostatic Protected Area) in compliance with IEC 61340-5-1 ESD Standard.
Okida production and warehouse areas are conditioned with special automatic air conditioning and humidification systems to ensure the necessary electronic production and the best ESD (electro-static discharge) conditions. Most recent SMD and TH lines are installed in special production areas, retrofitted with positive pressure system in order to keep the environment clean without dust and to provide the best temperature balance.
The SMT (Surface Mount Technology) assembly lines are an important strategic asset for the company, which invests every year in new machinery chosen from among the most advanced and reliable brands on the market.
The various phases (loader, screen print, 3D SPI, pick & place, reflow oven, 3D AOI) of the SMT process are supervised by control instruments.
The brand of the machinery and their configuration has been harmonized, with the aim of facilitating the process of technology transfer between the group's production sites.
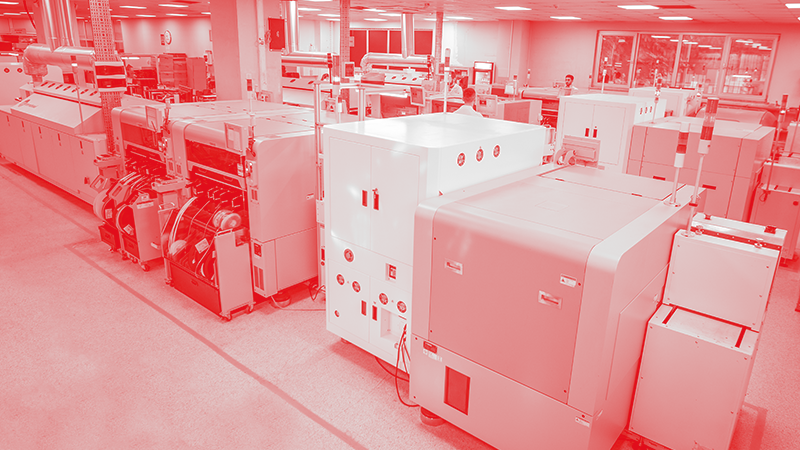
Allows you to check the correct deposit of the solder paste before placing the SMD component.
The machines are equipped with the most advanced technologies and allow real-time communication with the screen printer (backward) and pick & place (forward), in order to optimize the assembly process continuously.
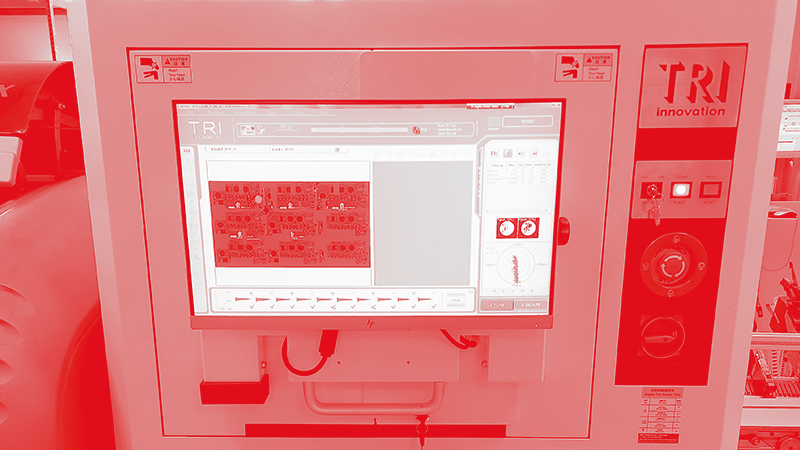
The 3D AOI optical inspection allows you to ensure the quality of the welds and the correct positioning of the SMD components on the board.

TH (Through Hole Technology) assembly lines use automatic wave welders positioned in line with the manual or automatic assembly stage of TH components. Okida's TH lines include automatic loader / unloader and AOI stage for optical inspection of all welds.
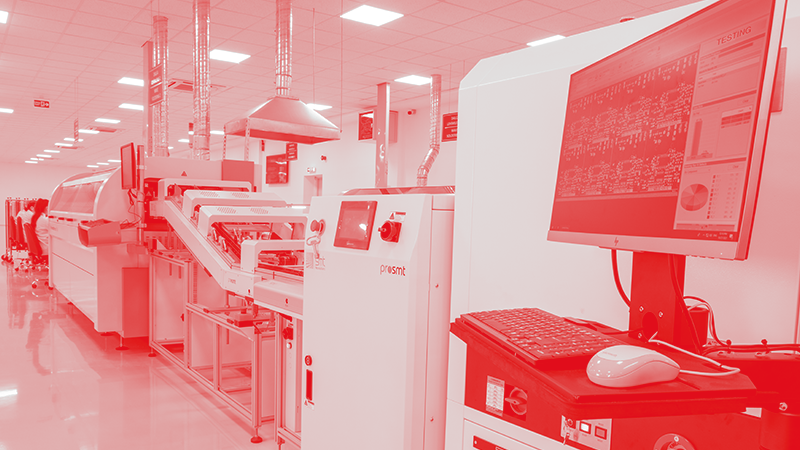
Parametric Test / In-Circuit-Test (ICT) technology is used to automatically test all components and nodes of the electrical circuit online. This guarantees 100% control coverage of all circuit parameters and allows to intercept any deviations from the nominal parameters. The programming of the microcontroller is carried out only after passing the ICT test with a positive result. Our ICT machines are multicore and allow you to test and program multiple devices in parallel. Once the product passes the ICT test, it is ready for the functional test.
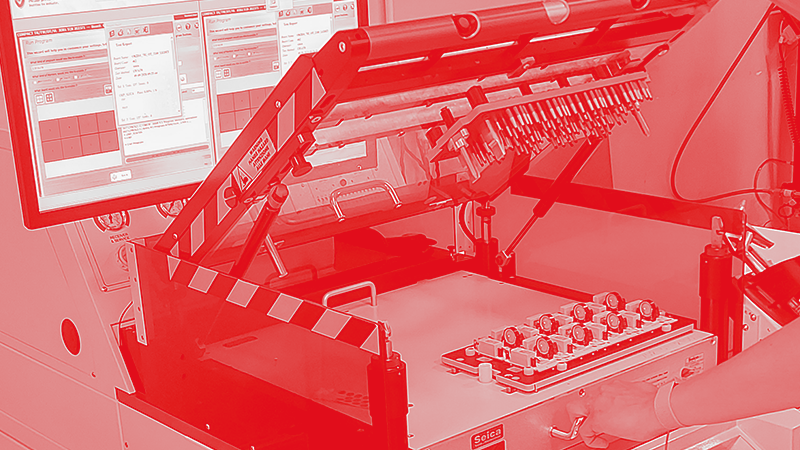
The functional testing of finished products is performed through testing systems designed and developed by Okida.
This procedure involves the drafting of a transparent protective film that adheres perfectly to the board and guarantees, by increasing its electrical insulation, protection against external factors such as humidity, dust, corrosion, etc. which can adversely affect its functionality. The application of the conformal coating is automated through machinery dedicated to the selective deposition of the conformal coating.
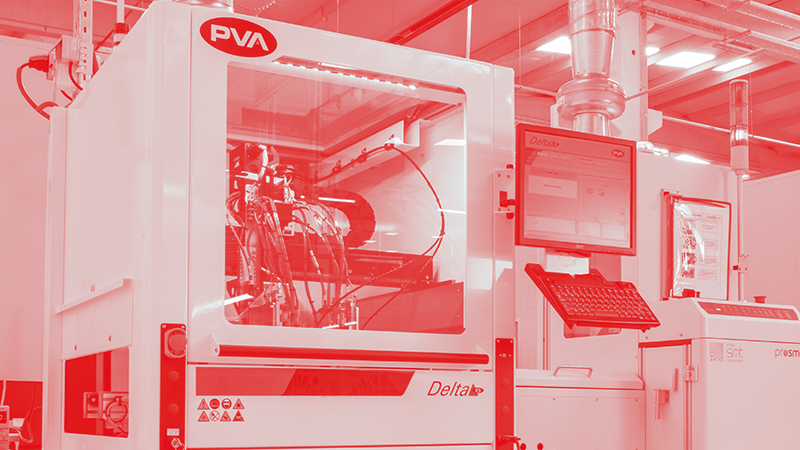